お探しのページが見つかりませんでした。
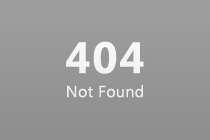
誠に申し訳ございませんがお客様がアクセスしようとしたページが見つかりませんでした。
以下の原因が考えられます。
- 一時的にアクセスできない状況にあるか、移動もしくは削除された可能性があります。
- Webブラウザのアドレスバー(URLを入力する欄)で、URLの綴りを誤って入力されている。
大変お手数ではございますが、次のいずれかの方法で、お求めの情報をお探しください。
キーワード検索
お求めの情報(キーワード)で検索することでお探しのページが見つかる場合があります。
サイトマップ
サイトマップからサイト全体を見渡せます。全情報から探すことで目的のページが見つかる場合があります。
お問い合わせ
製品・サービスについてのご質問・ご相談はお気軽にお問い合わせください。